Ever wonder about the nuts and bolts behind nearly everything we use every single day? It's a pretty fascinating subject, actually. Think about your phone, that coffee cup, or even the chair you're sitting on. None of these things just magically appear. There's a whole process, a lot of careful work, that makes them real. And at the heart of that making, you'll find something called tooling. It's a basic concept, but so important.
So, we hear the word "tooling" tossed around, especially when people talk about factories or making things. But what does it really mean? For many of us, it's a bit of a mystery, a word that sounds technical and maybe a little bit dry. However, once you pull back the curtain just a little, you discover it's about the clever ways we create the very instruments that help us build all sorts of products. It's a fundamental step, really, in bringing ideas to life.
This idea of tooling, you know, it's not just for the folks working in big industrial places. It’s a concept that touches so many parts of our modern world. If you're someone who likes to know how things work, or perhaps you're just curious about the stuff that goes on behind the scenes, getting some clear explanations about tooling can be really helpful. It’s about getting those good, solid tooling u answers that make sense.
Table of Contents
- What's the Real Deal with Tooling?
- Why Does Tooling Matter So Much?
- What Kinds of Tooling Are There?
- How Do Soft and Hard Tooling Differ?
What's the Real Deal with Tooling?
So, what exactly is tooling, when you get right down to it? Well, it's pretty much about creating the special pieces of equipment and the various bits of gear that you need for making things. Think about it like this: if you want to bake a cake, you need a pan, right? That pan, in a very simple way, is a tool for making the cake. In the world of making products, tooling is that process of making the "pans" – or the molds, the jigs, and the fixtures – that are absolutely necessary for a production line to work. It’s about building the very things that shape other things. That, is that, it's a fundamental part of how items are put together.
When folks talk about tooling, they're often talking about the whole thought process and the work involved in coming up with and building the instruments that are going to be used in a factory. It's the core support for how manufacturing operations run. Without these special tools, it would be extremely hard, if not impossible, to make anything consistently or at a large scale. It's the initial step that makes all the later steps possible. You know, it's like setting up your kitchen with all the right gadgets before you start cooking a big meal. You need the right setup.
Tooling, which people sometimes call machine tooling, is also the process where you give materials a particular shape or form so they turn into parts that fit together perfectly. These parts have to be made with a very specific size and shape, often within tiny allowances. It's about taking raw stuff and transforming it into something useful and exact. For instance, imagine you need a specific metal piece for an engine. Tooling is how you get that metal piece to be exactly the right shape and size, every single time. It's a very precise sort of work.
- Chip And Joanna Gaines Net Worth
- Jayden Daniels Education
- Odessa Azion
- How Old Is Doctor Phil
- Attack On Titan Levi
Getting Your Tooling U Answers on Basic Concepts
In its most straightforward sense, tooling means planning out, putting together the designs for, and actually building the instruments that are going to be needed to make different parts or components. It's about making the tools that make the parts. It's a bit like an artist preparing their brushes and canvas before they start painting a picture. They need the right tools for the job, and someone has to make those tools. This is where tooling comes in. It's the initial step in a much larger process, and it's absolutely essential for getting things right from the start. We, like your, need to get these fundamental tooling u answers clear.
This work, you know, it's also known as machine tooling. It involves taking materials and carefully shaping them, cutting them, and forming them into the pieces that will then be used to create finished products and all their individual bits. It's the hands-on part of making sure that every single piece comes out just as it should. Think about a piece of wood that needs to become a chair leg. Tooling is the way you make sure that leg is the correct length, the correct thickness, and has the right connections to fit with the rest of the chair. It's a very detailed kind of work, pretty much.
Sometimes, tooling is described as the process of shaping materials, mostly to create accurate and one-of-a-kind parts. These parts are usually defined by very specific allowances, meaning they have to be made within a tiny range of acceptable sizes or shapes. It's about achieving consistency and precision on a large scale. For example, if you're making a thousand identical screws, tooling is the method that ensures every single one of those screws is exactly the same as the last. It’s about making sure everything fits together perfectly, every time. That, is that, it helps us keep things uniform.
Why Does Tooling Matter So Much?
You might be wondering why all this talk about tooling is such a big deal. Well, honestly, tooling is pretty much the backbone of how things get made. Without the right tools, it's incredibly hard to produce anything consistently or efficiently. Think of it this way: if you're building a house, you need hammers, saws, and drills, right? Tooling is the process of making sure those hammers, saws, and drills are available and perfectly suited for building that particular house. It's what allows a factory to turn raw materials into finished goods that people can actually use. It’s about making sure the whole system can operate smoothly, basically.
The ability to create specific tools for specific jobs means that products can be made with high levels of exactness. This is incredibly important for things that need to fit together perfectly, like the parts of an engine or the components of a complex electronic device. If the tools aren't made well, then the parts they produce won't be made well either, and that can lead to all sorts of problems down the line. It's about setting up the conditions for success right from the very beginning. You know, it's like having a really good recipe and the right cooking tools to make a delicious meal. The tools make a huge difference.
Moreover, tooling allows for the mass production of items. Once a tool, like a mold for a plastic toy, is created, it can be used repeatedly to make thousands, even millions, of identical toys. This brings down the cost of each individual item, making products more affordable for everyone. It's what makes our modern consumer world possible, in a way. Without the careful work of tooling, many of the things we take for granted would be far too expensive to produce on a wide scale. It’s a pretty important economic driver, too, it's almost.
Finding Tooling U Answers on Manufacturing's Core
Tooling, you know, it’s really about building various kinds of equipment and gear that are absolutely necessary for production. This includes things like molds, which are used to shape liquid materials as they cool and harden, or jigs and fixtures, which hold pieces in place while they're being worked on. These aren't just general tools; they are often very specific to the product being made. For example, a mold for a car door handle is very different from a mold for a plastic bottle cap. It's about having the right specialized equipment for every single part. So, to be honest, it's a very specific kind of preparation.
In its most simple form, a tool is just something that helps you work or helps you make something. It's an aid that you need to create a product or a part. These can include things like dies, which are used to cut or shape material, or gauges, which are used to measure things very precisely. Molds, as we mentioned, are for shaping. Jigs hold work in place, and cutting tools, well, they cut. Each one has a very specific purpose in the manufacturing process. It's like having a full set of specialized screwdrivers, each one for a particular type of screw. You need the right one for the job, pretty much.
The whole process of tooling is often referred to as machine tooling, which just highlights that many of these tools are used with machines to perform their functions. Whether it's a mold for injecting plastic or a cutting tool on a milling machine, these tools are what allow the machines to do their work accurately and repeatedly. It's the interaction between the human design of the tool and the mechanical action of the machine that makes modern manufacturing so effective. You know, it's a collaboration between human ingenuity and mechanical muscle. Getting these tooling u answers helps you see the bigger picture.
What Kinds of Tooling Are There?
When we talk about tooling, it's not just one big, general thing. There are different types, each with its own special purpose. For instance, you might hear about molds, which are used to create specific shapes by pouring material into them. Think about how a plastic toy is made – liquid plastic goes into a mold, cools, and comes out as a toy. Then there are dies, which are often used to cut or shape metal, like punching out a specific shape from a sheet of steel. And of course, there are cutting tools, which are pretty much what they sound like – tools designed to cut away material to get a desired shape. So, actually, it's quite a varied field.
Each type of tooling serves a particular function in the process of making things. Molds are essential for anything that needs to be formed from a liquid or pliable material, like plastics, rubber, or even some metals. Dies are fundamental for stamping, bending, or cutting operations, especially in metalworking. Cutting tools are used across almost every type of manufacturing, from machining metal parts to shaping wood or composite materials. The choice of tool depends entirely on the material being used and the final shape or function of the part. It's about picking the right instrument for the job at hand, you know, very specifically.
It's important to remember that these tools are themselves products of a very careful design and making process. They aren't just off-the-shelf items for the most part. They are specifically created to produce a certain part with a certain level of precision. This means that the tooling itself requires a lot of skill and specialized equipment to create. The quality of the final product often depends directly on the quality of the tools used to make it. So, in a way, the tools are just as important as the things they produce. They are, really, the unsung heroes of manufacturing.
Your Tooling U Answers for Different Tool Types
To give you some more tooling u answers about the different kinds, let's consider some examples. You have molds, which are pretty common for anything from plastic bottles to car dashboards. They allow for the creation of complex, hollow, or intricate shapes. Then there are jigs, which are devices that hold a workpiece and guide a tool for a specific operation, like drilling a hole in exactly the right spot. Fixtures are similar; they hold a workpiece in a fixed position for a particular operation, but they don't usually guide the tool itself. They are about stability and repeatability. Basically, they make sure things are held steady.
Cutting tools are another broad category. These can be anything from drill bits that make holes to milling cutters that shape surfaces, or even specialized blades for slicing materials. The exact design of a cutting tool depends on the material it's meant to cut and the kind of cut it needs to make. For instance, a tool for cutting steel will be very different from one used for cutting soft plastic. It’s all about the specifics of the task. That, is that, every detail counts.
Dies are often used in processes like stamping or forging. A stamping die, for example, can cut out shapes from a metal sheet or bend it into a specific form with one swift press. Forging dies are used with immense pressure and heat to shape metal. These tools are incredibly strong and built to withstand tremendous forces. They are about transforming materials through pressure and precise shaping. You know, it's like a giant cookie cutter for metal, in a way.
How Do Soft and Hard Tooling Differ?
When you're making a product, especially a new one, you might hear about "soft tooling" and "hard tooling." These are two different approaches to making the tools themselves, and they're chosen based on what you're trying to achieve at a particular stage of production. Soft tooling is generally used when you're still working out the kinks, maybe perfecting a design or creating a few prototypes. It's a bit like making a temporary sketch before you commit to a full painting. It allows for changes and adjustments without a huge investment. It's often quicker and less costly to create these temporary tools. So, it's almost like a trial run.
Soft tooling often involves materials that are easier to work with and less expensive, or processes that are faster to set up. This might mean using simpler molds or less durable materials for the tools themselves. The goal here isn't to make millions of parts, but rather to make a small batch, test them out, and see if the design works as intended. If you find a problem, it's much easier and cheaper to change a soft tool than a hard one. It's about flexibility and learning. You know, it's like building a model before you construct the real building.
Hard tooling, on the other hand, is the method you'll need when it's time to finish up a product's design and produce much larger quantities. This is when you're confident in your design and you need tools that can stand up to repeated use over a long period. These tools are made from very strong, durable materials, often metals, and are built to last. They are designed for high-volume production, where consistency and longevity are key. It’s a significant investment, but it pays off when you're making a lot of something. Basically, it's for when you're ready to go all in.
More Tooling U Answers - Soft vs. Hard Approaches
To give you more tooling u answers, think about the lifespan and cost. Soft tooling usually has a shorter lifespan and is less expensive to make. It's ideal for those early stages of product creation, for testing concepts, or for producing a limited number of items for market research. If you only need a few hundred pieces, soft tooling might be the way to go because the initial cost is lower. It provides a way to get products into people's hands relatively quickly to get feedback. It's a pretty practical approach for new ideas.
Hard tooling, however, involves a much bigger upfront cost and takes more time to create. But once it's made, it can produce parts for years, sometimes even decades, without significant wear. This makes it extremely cost-effective for large production runs where millions of identical parts are needed. The precision and durability of hard tools mean that every single part coming off the line will be virtually identical, meeting those strict quality requirements. It's about achieving consistency at a very large scale. You know, it's like building a factory that will run for a long, long time.
The choice between soft and hard tooling really depends on the project's stage and its overall goals. If you're still experimenting and need to make changes, soft tooling offers the necessary freedom. If you're ready to go to market with a final product and produce it in massive quantities, then hard tooling is the way to ensure efficiency and quality over time. It’s a very strategic decision, actually, that impacts the entire production timeline and budget. Getting these distinctions clear helps you understand the whole picture of manufacturing processes.
This discussion has helped us get a better handle on what tooling means, why it's so important for making things, the different kinds of tools involved, and how the "soft" and "hard" approaches differ. It’s all about creating the right instruments to build the items we use every single day, making sure they are made with care and precision.
Related Resources:
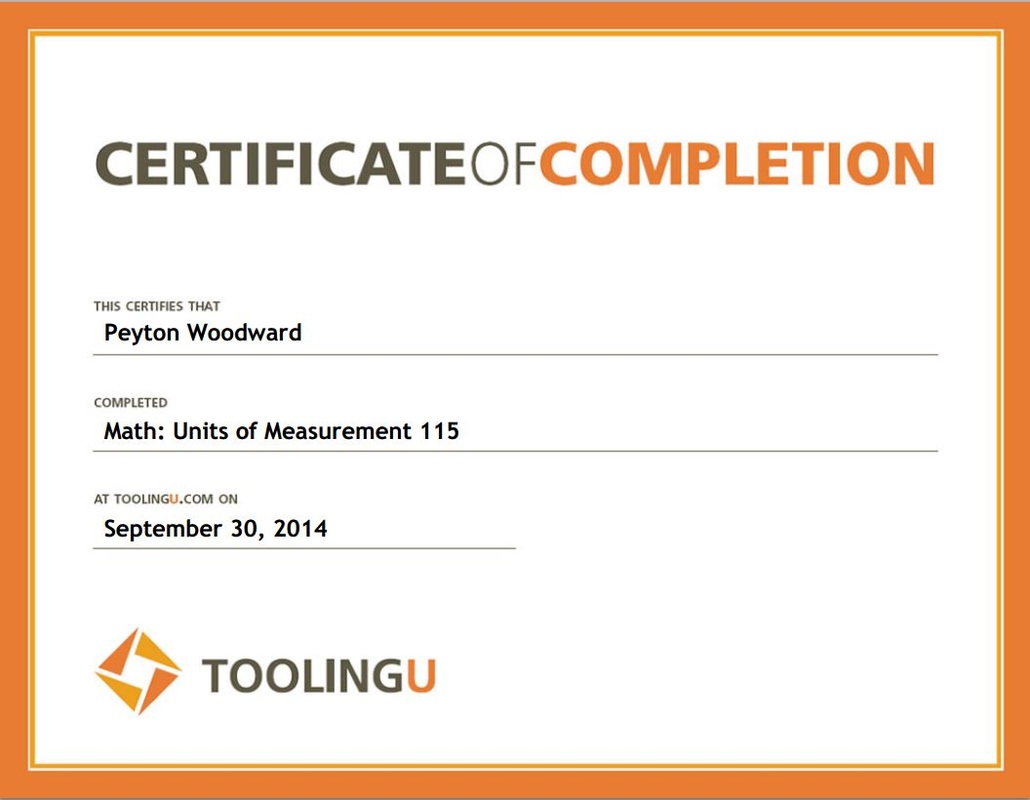


Detail Author:
- Name : Savanna O'Conner
- Username : gerhard67
- Email : alf.farrell@hotmail.com
- Birthdate : 1982-12-08
- Address : 462 Leo Circle Suite 063 West Jarrettberg, DE 30716-1152
- Phone : 838.778.3804
- Company : Aufderhar Group
- Job : Engineering Manager
- Bio : Ipsa blanditiis ratione ducimus veniam itaque. Repellat officia ut quo reprehenderit. Qui nihil quis quod placeat dicta ut voluptatibus. Aut officiis recusandae eum.
Socials
twitter:
- url : https://twitter.com/lela9030
- username : lela9030
- bio : Omnis ab aperiam facilis officia soluta et. Blanditiis sed pariatur ut dolor possimus unde.
- followers : 4904
- following : 1086
tiktok:
- url : https://tiktok.com/@leladare
- username : leladare
- bio : Provident quam deleniti eaque dolorem hic qui tempora saepe.
- followers : 378
- following : 1812
facebook:
- url : https://facebook.com/darel
- username : darel
- bio : Est et quidem vero id eos itaque neque.
- followers : 5345
- following : 391
linkedin:
- url : https://linkedin.com/in/lela_dare
- username : lela_dare
- bio : Non fuga nihil alias.
- followers : 4828
- following : 1978
instagram:
- url : https://instagram.com/lela_id
- username : lela_id
- bio : Sint dolorum fuga maxime nulla fugiat. Omnis ea qui sit eius temporibus temporibus.
- followers : 849
- following : 58